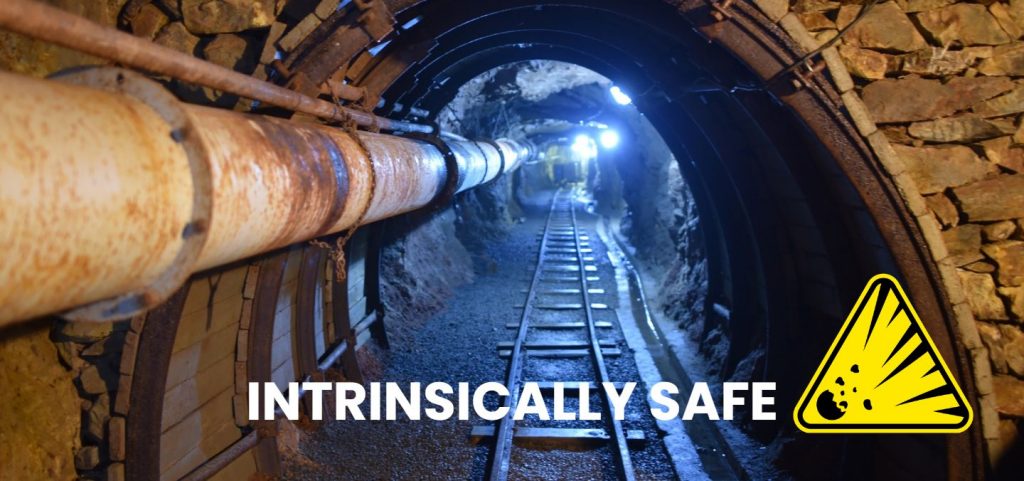
Welcome to our comprehensive guide on intrinsic safety! If you’ve ever wondered how certain devices can operate in hazardous environments without causing explosions or fires, then you’re in the right place. Intrinsic safety is a fascinating concept that allows equipment to be used safely in potentially explosive atmospheres. Whether you work in industries such as oil and gas, mining, chemical processing, or any other high-risk environment, understanding intrinsic safety is crucial for maintaining a safe working environment. So let’s dive right into this intriguing topic and demystify the world of intrinsic safety together!
What is intrinsic safety?
Intrinsic safety is a design concept that ensures electrical equipment can be used in hazardous environments without causing sparks or ignition. It involves limiting electrical energy and preventing it from reaching levels that could ignite flammable gases, vapors, or dusts. This is achieved by using specially designed intrinsically safe devices that have low power outputs and are incapable of generating enough energy to cause an explosion.
The key idea behind intrinsic safety is to eliminate potential sources of ignition by controlling the amount of electrical energy present in a device. By employing various protective measures such as current-limiting resistors, zener diodes, and galvanic isolation barriers, intrinsic safety minimizes the risk of fire or explosion.
To ensure compliance with intrinsic safety standards, devices undergo rigorous testing and certification processes conducted by authorized bodies like UL (Underwriters Laboratories) or ATEX (Atmosphères Explosibles). These certifications provide assurance that the equipment meets stringent safety requirements for use in specific hazardous locations.
The History of Intrinsic Safety
The history of intrinsic safety is a fascinating journey that dates back several decades. It all began in the early 20th century when industries like mining, oil and gas, chemicals, and manufacturing were faced with the challenge of operating electrical equipment safely in hazardous environments.
In those days, traditional methods such as explosion-proof enclosures were used to protect electrical devices from igniting flammable gases or dust particles. However, these solutions often involved bulky designs and increased costs.
In the 1940s, engineers started developing a new concept called “intrinsic safety.” This approach aimed to prevent electrical equipment from producing sparks or temperatures high enough to ignite explosive atmospheres. The idea was simple yet revolutionary – limit electrical energy levels to safe values.
Over time, international standards for intrinsic safety emerged. Organizations like the International Electrotechnical Commission (IEC) developed guidelines that defined criteria for intrinsically safe systems and components.
Advancements in technology enabled manufacturers to design smaller and more efficient intrinsically safe devices. Today, these devices are widely used in various industries where explosive hazards exist – providing reliable protection while minimizing risks.
Explosive Atmosphere Presence | Explosive Atmosphere Nature | Area Classification | Group | EPL |
---|---|---|---|---|
Long Periods/Continuously | Coal Mine | – | I | Ma |
Gas | zone 0 | II(IIA,IIB,IIC) | Ga | |
Dust | zone 20 | II(IIA,IIB,IIC) | Da | |
Occasionally During Normal Operation | Coal Mine | – | I | Mb |
Gas | zone 1 | II(IIA,IIB,IIC) | Gb | |
Dust | zone 21 | II(IIA,IIB,IIC) | Db | |
Not During Normal Operation | Gas | zone 2 | I | Gc |
Dust | zone 22 | II(IIA,IIB,IIC) | Dc |
Table 1: Hazardous Areas Classification Summarizing Table
Note: Area Classification Derived from IEC 60079-10-1 (for gas) and IEC 60079-10-2 (for dust) and minimum Equipment Protection Level of products that could be installed.
A Zone defines the frequency and duration of the occurrence of an explosive atmosphere. The Zone system has 3 levels of hazard for gas or dust.
Gases, Vapors and Mists (IEC 60079-10-1 Classification of areas – Explosive gas atmospheres):
· Zone 0: Ignitable concentrations of flammable gases or vapors which are present continuously or for long periods of time
· Zone 1: Ignitable concentrations of flammable gases or vapors which are likely to occur under normal operating conditions
· Zone 2: Ignitable concentrations of flammable gases or vapors which are not likely to occur under normal operating conditions and do so only for a short period of time.
Dusts (IEC 60079-10-2 Classification of areas – Combustible dust atmospheres):
· Zone 20: An area where combustible dusts or ignitable fibers and flyings are present continuously or for long periods of time.
· Zone 21: An area where combustible dusts or ignitable fibers and flyings are likely to occur under normal operating conditions.
· Zone 22: An area where combustible dusts or ignitable fibers and flyings are not likely to occur under normal operating conditions and do so only for a short period of time.
How does It Work?
How does intrinsic safety work? It’s a question that many people have when they first encounter this concept. Intrinsic safety is a method of ensuring that electrical equipment can be used safely in hazardous environments, where the risk of explosions or fires is high.
At its core, intrinsic safety works by limiting the energy available to electrical devices so that it cannot ignite flammable substances in the environment. This is achieved through several key principles and techniques.
All components of an intrinsically safe system are designed to operate at low levels of power and voltage. By keeping these values below certain thresholds, the risk of sparks or heat generation is greatly reduced.
Each component within an intrinsically safe system must be carefully chosen and approved for use in hazardous environments. This involves selecting materials with low ignition potential and ensuring proper insulation and protection against dust or moisture.
Intrinsically safe systems employ various means to limit electrical energy flow such as current-limiting resistors or galvanic isolation barriers. These measures prevent excessive current from flowing through circuits, reducing the likelihood of ignition.
In addition to these design considerations, intrinsic safety also requires strict adherence to installation guidelines and maintenance practices. Proper grounding techniques are essential for dissipating any accumulated charge, while regular inspections ensure ongoing compliance with safety standards.
Understanding how intrinsic safety works provides insight into why it is such an effective approach for protecting against explosions in hazardous environments. By focusing on minimizing energy levels and employing robust design principles, this methodology ensures that electrical equipment can be used safely without compromising productivity or efficiency.
The Challenges of Intrinsic Safety
Challenges often accompany any technological solution, and intrinsic safety is no exception. While it offers numerous advantages, there are some obstacles to overcome when implementing this approach in hazardous environments.
One of the primary challenges of intrinsic safety is ensuring compatibility between equipment. Intrinsic safety requires all components within a system to be certified as intrinsically safe. This means that each device must meet specific standards and be designed to operate safely within the prescribed parameters. Achieving this level of compatibility can be complex and time-consuming, especially in situations where different manufacturers’ devices need to work together seamlessly.
Another challenge lies in the limited power available for intrinsically safe devices. In order to prevent ignition sources, such devices are designed with low energy levels. This means they may have limited functionality compared to non-intrinsically safe alternatives. Additionally, powering multiple devices or operating them over long distances may require additional planning and consideration.
Furthermore, maintenance and repair procedures for intrinsically safe equipment can pose challenges due to their specialized nature. Technicians working on these systems must have adequate training and knowledge about intrinsic safety requirements and regulations.
Cost considerations can also present a challenge when implementing intrinsic safety measures. Intrinsically safe equipment tends to be more expensive than its non-intrinsically safe counterparts due to the additional engineering involved in ensuring compliance with safety standards.
Despite these challenges, many industries recognize the importance of intrinsic safety in protecting personnel and assets from potential hazards. With advancements in technology and ongoing research efforts focused on addressing these obstacles, it is expected that future iterations will bring solutions that make implementation easier while maintaining high levels of safety.