In the era of innovation and technology, industrial automation has become a buzzword for its immense potential to revolutionize manufacturing and production processes. Unlike manual labour, industrial automation allows machines to perform tasks with precision and consistency, resulting in increased efficiency, cost-saving benefits, and improved productivity. In this blog post, we will dive into the world of industrial automation – from its history to future trends – exploring how it has transformed industries around us. So fasten your seatbelts as we embark on an exciting journey through the realm of Industrial Automation!
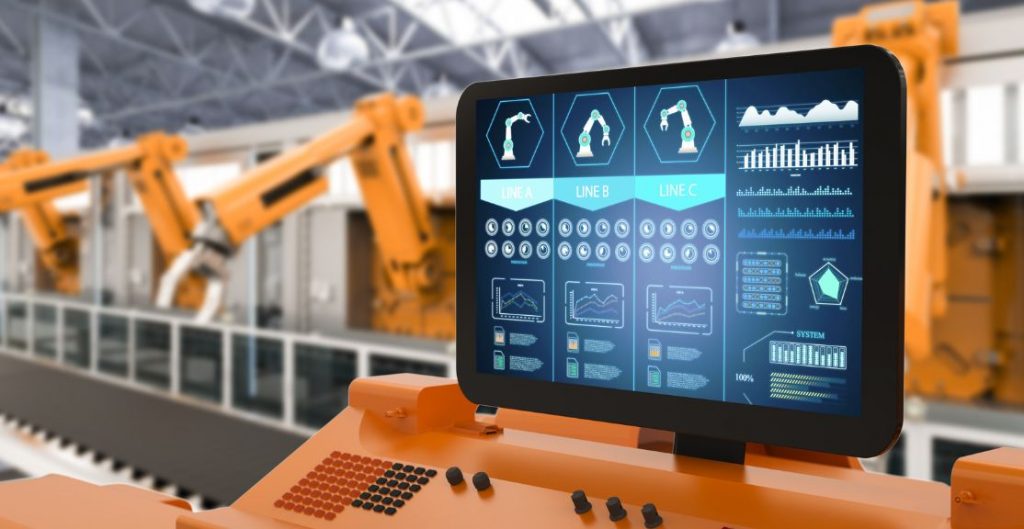
What is Industrial Automation?
Industrial automation is the use of technology and machinery to perform tasks that were previously done manually by human workers. It involves the integration of various technologies such as artificial intelligence, robotics, sensors, and software systems into manufacturing processes. The primary goal of industrial automation is to streamline production processes while improving efficiency and productivity.
One key aspect of industrial automation is that it reduces the need for manual labour – this can be particularly useful in industries where repetitive or hazardous tasks are involved. By automating these tasks with machines, companies can minimize worker injury risks while also reducing labour costs.
Industrial automation includes various applications across different industries such as automotive manufacturing, food processing, aerospace engineering, pharmaceuticals etc. In fact, almost every industry today uses some form of industrial automation to improve their productivity levels.
Industrial Automation has become an essential part of modern-day production processes due to its many benefits like increased efficiency & accuracy and reduced operational cost & downtime.
Future-Proofing Your Industrial Automation Network



The History of Industrial Automation
The history of Industrial Automation dates back to the 18th century when power-driven machines were invented. However, it wasn’t until the 20th century that industrial automation took off. The first programmable logic controllers (PLCs) were introduced in the late ’60s and proved to be a breakthrough in automating manufacturing processes.
In the ’70s and ’80s, computer technology became more advanced and was incorporated into industrial processes. With this came an increase in efficiency and productivity as well as a decrease in production costs.
The use of robots for automation also began during this time period. Initially used for repetitive tasks like welding or painting, robots have become sophisticated enough to handle complex operations such as assembly line work.
Over time, developments like machine learning algorithms have given rise to intelligent systems capable of predicting downtime before it happens while optimizing production capacity.
Today, we see rapid advancements being made with technologies like artificial intelligence (AI), cloud computing, big data analytics making their way into smart factories where machines can communicate with one another seamlessly without human intervention.
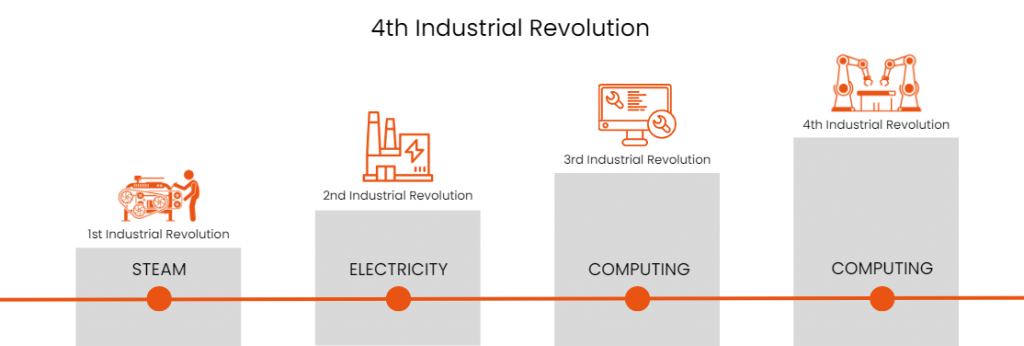
The Different Types of Automation Systems
There are various types of industrial automation systems available today that can be used to optimize production processes. One type is fixed automation, which involves using specialized equipment to complete a specific task repeatedly. Fixed automation is commonly used in industries such as chemical manufacturing and food processing.
Another type is programmable automation where machines can be programmed to perform multiple tasks without the need for human intervention. Programmable logic controllers (PLCs) are often used in this type of automation system.
Flexible automation refers to a system that has been designed with flexibility in mind, allowing it to adapt easily to changes in product design or specifications. This type of system typically uses robotics and computer-controlled equipment, making it ideal for high-volume production environments.
Integrated Automation combines different types of automated systems into one cohesive unit that works together seamlessly, providing greater efficiency and productivity than any single component could achieve on its own.
Collaborative robots or “cobots” work alongside humans safely while still completing repetitive or dangerous tasks quickly and efficiently. As technology advances at an unprecedented rate, we can expect even more innovative types of industrial automation systems to emerge in the coming years.
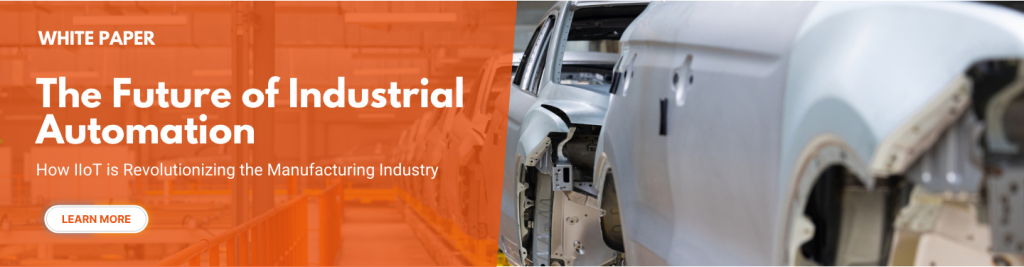
How has automation affected the industry?
Automation has had a profound impact on the industrial sector. With the introduction of automated systems, industries have been able to improve their productivity, reduce costs and increase efficiency. One of the most significant impacts of automation on the industry has been the ability to produce goods in large quantities at a much faster rate than was previously possible.
Automated systems have revolutionized manufacturing processes by enabling factories to operate continuously without interruption or downtime. This means that production can continue around the clock, leading to an exponential increase in output capacity. As a result, industries are now able to meet customer demand more quickly and efficiently than ever before.
Automation has also led to increased safety standards within many industrial environments. By eliminating human error from dangerous tasks such as heavy lifting or hazardous material handling, workplaces are now safer for employees while also reducing liability risks for companies.
In addition, automation allows for more precise control over production processes which leads to higher quality products being produced with less waste generated during production cycles – this benefits both manufacturers and consumers alike.
It is clear that automation has had an overwhelmingly positive impact on the industry by improving efficiency, and increasing productivity levels while ensuring worker safety remains paramount throughout any process changes implemented through these technologies!
What is time-sensitive networking for industrial automation?
Time Sensitive Networking (TSN) is a technology that allows for real-time communication in industrial automation systems. It ensures that critical data is delivered within strict time constraints, which helps to reduce latency and improve efficiency. TSN is essential for applications where timing is critical, such as motion control or process automation.
One of the key benefits of TSN is its ability to synchronize devices across an entire network, ensuring that all components are working together seamlessly. This synchronization eliminates delays and ensures that processes happen precisely when they need to.
TSN also provides deterministic communication, meaning that messages are delivered predictably without any interference from other traffic on the network. This reduces the likelihood of collisions and retransmissions, which can cause delays and decrease overall system performance.
Time-sensitive networking has become increasingly important in modern industrial environments as it enables precise synchronization between different machines while improving system reliability by reducing latencies through deterministic communication protocols.
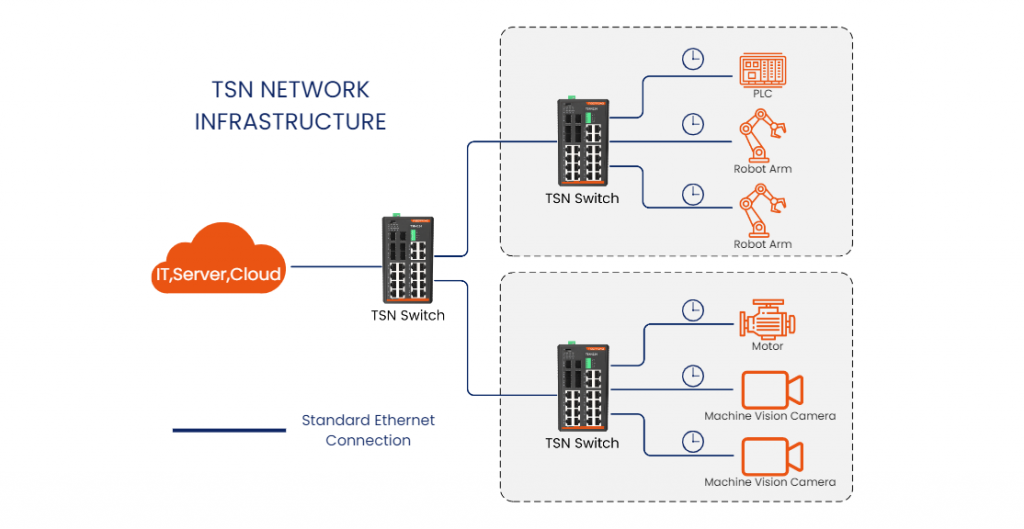
The Future of Industrial Automation
The future of industrial automation is exciting and full of potential. With advancements in technology, there are endless possibilities for what can be achieved through automation. Robotics and artificial intelligence (AI) will play a major role in shaping the future of industrial automation.
One area where we can expect to see significant improvements is in safety. Robots equipped with sensors and cameras will be able to detect potential hazards before they occur, preventing accidents from happening. In addition, robots will be able to perform tasks that are too dangerous for humans, such as working with hazardous chemicals or handling heavy machinery.
Another benefit of industrial automation is increased efficiency. Automated systems can work around the clock without taking breaks or getting tired, which means production times can be significantly reduced. This leads to faster turnaround times and lower costs for businesses.
Moreover, AI algorithms will continue to improve over time, allowing machines to make more complex decisions independently without human intervention. This could lead to even more advanced forms of automation that we haven’t yet imagined.
However, some concerns have been raised about the impact on jobs due to increasing levels of automation. As machines become more intelligent and capable, it’s possible that certain job functions may become obsolete or unnecessary altogether.
Though, the future looks bright for industrial automation as it continues to evolve at an unprecedented pace providing benefits such as improved safety measures and increased efficiency rates while addressing lingering concerns related mainly towards employment opportunities created by these changes in technology trends within this space!