In the realm of industrial automation, reliable and high-performance communication is the backbone of efficient operations. Two terms frequently encountered – Ethernet and PROFINET – often confuse: are they competitors, or do they work together? Understanding their relationship is crucial for designing robust control systems. While Ethernet provides the universal physical and data link foundation (the wires, switches, and basic data framing), PROFINET is a sophisticated, application-layer industrial protocol that builds upon this standard Ethernet infrastructure. This article delves into their key differences, exploring how PROFINET transforms standard Ethernet into a deterministic, real-time network capable of meeting the stringent demands of modern factories, from high-speed motion control to seamless integration and advanced diagnostics, while still leveraging the ubiquity and cost-effectiveness of Ethernet technology.
What is the PROFINET Protocol?
PROFINET is a high-performance industrial Ethernet communication protocol designed specifically for automation. Built upon standard Ethernet hardware (cables, switches), it extends the technology with critical features essential for industrial control, such as deterministic real-time communication for precise synchronisation of machines and processes. PROFINET operates across the higher layers of the communication stack (above the Ethernet physical and data link layers), defining application profiles, services, and device behaviours. It supports various communication classes, including TCP/IP for non-time-critical data, Real-Time (RT) for fast cyclic data, and Isochronous Real-Time (IRT) for motion control requiring extreme precision and jitter below 1 µs. Key strengths include integrated diagnostics for rapid troubleshooting, simplified engineering and configuration (often leveraging existing IT tools), seamless integration with legacy PROFIBUS systems via proxies, and high scalability from simple sensors to complex motion control systems, significantly enhancing productivity and reducing downtime in manufacturing environments. It is standardised in IEC 61158 and IEC 61784.
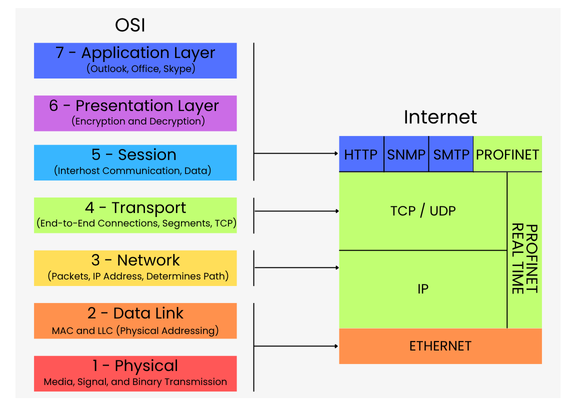
PROFINET is a communication protocol that lives at layer seven of the ISO/OSI model, the seven-layer model that generically describes the abstraction layers of a communication system.
Key Differences between PROFINET and Ethernet
While PROFINET utilises standard Ethernet hardware (cables, switches, NICs), it represents a specialised industrial communication protocol built on top of Ethernet, designed specifically for the demanding requirements of automation. The core differences lie in their purpose and capabilities: Standard Ethernet focuses on general-purpose, best-effort data delivery in office/IT environments, tolerating variable delays (non-determinism). In contrast, PROFINET adds critical industrial features like guaranteed real-time communication (determinism) for precise synchronisation of machines and processes, integrated device diagnostics, simplified configuration mechanisms, and seamless integration with existing PROFIBUS systems. Essentially, Ethernet provides the foundational physical and data link layers, while PROFINET defines the higher-layer application protocol, services, and profiles tailored for robust, high-performance industrial control.
Compatibility and Integration between PROFINET and Ethernet
PROFINET Runs ON Ethernet: PROFINET is not a replacement for the physical and data link layers (Layer 1 & 2 of the OSI model); it’s a higher-layer industrial protocol (Layers 7, and parts of 3/4) that depends on standard Ethernet hardware (Cat5e/6 cables, industrial Ethernet switches, Ethernet ports on devices). So, the Ethernet physical network is fundamentally required.
- TCP/IP Coexists (and is Often Used): While PROFINET handles the critical, deterministic real-time communication (RT/IRT) for control loops and I/O data, standard Ethernet. TCP/IP communication typically runs simultaneously on the same physical network for non-time-critical tasks. This includes:
- Configuration & Diagnostics: Engineering tools (like TIA Portal) use TCP/IP to discover devices, download configurations, and access detailed diagnostic web pages hosted on PROFINET devices.
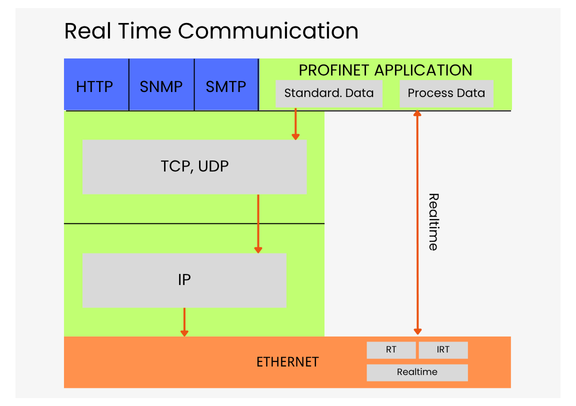
- HMI Communication: Operator panels (HMIs) often use TCP/IP (e.g., OPC UA, HTTP) to communicate with PLCs or directly access data from devices for visualisation.
- Integration with IT Systems: Connecting to plant networks, databases, MES/ERP systems, or remote access for maintenance usually relies on TCP/IP.
- File Transfer: Uploading and downloading programs, firmware updates, or recipe data often utilise protocols such as FTP or HTTP over TCP/IP.
- Device Web Servers: Most modern PROFINET devices have built-in web servers (accessible via HTTP/HTTPS) for monitoring and diagnostics, which require TCP/IP.
In essence, the automation network is a single, converged Ethernet infrastructure. PROFINET is the protocol handling the critical real-time automation traffic over this Ethernet infrastructure. TCP/IP is the protocol also running over the same infrastructure to handle all the necessary configuration, diagnostics, HMI, and IT integration tasks. You need the Ethernet hardware foundation for both. PROFINET doesn’t eliminate the need for TCP/IP services in a practical industrial network; it efficiently shares the physical network with them while ensuring its real-time performance isn’t compromised.