Hey there! Are you an industrial networking specialist who’s sick of getting your top-notch products rejected because of EMI, EMC, and ESD issues? I feel your pain. We’ve all been there – spending months perfecting a new device only to have international regulators reject it over some obscure electromagnetic compliance regulation.
Well, suffer no more! In this article, I’ll break down the causes of these electrostatic and electromagnetic interference issues in plain English. More importantly, I’ll give you pro tips to avoid those pesky rejections so you can get your innovative products to market faster. Stick with me, and you’ll be an EMI, EMC, and ESD expert in no time!
Understanding EMC, EMI and ESD Standards for Industrial Networking Equipment
If you design industrial networking equipment, you need to understand electromagnetic compatibility (EMC), electromagnetic interference (EMI) and electrostatic discharge (ESD) standards. These regulate how much radiation your product emits and how much it can withstand without permanent damage. Major standards include FCC in the US, CE in Europe and VCCI in Japan.
EMC and EMI
EMC ensures your product doesn’t unintentionally emit radio frequency waves that could interfere with other electronics. EMI refers to radio frequency waves emitted by other devices that could disrupt your product. Standards specify maximum emission and immunity levels. Exceeding them could result in product rejection, especially for global markets.
ESD
ESD refers to static voltage built up on the human body and discharged when touching your product. Standards define voltage levels your product should withstand without failure. ESD is often overlooked but critical for reliability and safety.
Designing for Compliance
The best approach is to design for the worst-case standard limits, though costs may be higher. At a minimum, you need to meet the requirements of your target markets. Redesigning for new markets later is inefficient.
Consider EMC, EMI and ESD early in the design process. Use good PCB layout, filtering, shielding and ESD protection devices. For EMI, choose components and cables that emit less radiation. Proper grounding, bonding and cable routing also help. ESD-safe manufacturing and handling procedures are important too.
Testing is critical to ensure compliance before going to market. Work with accredited test labs to measure emission and immunity levels. Fix any issues and retest as needed. Compliance certification can then be obtained to legally sell your product.
Meeting EMC, EMI and ESD standards requires diligence but allows you to build reliable, interoperable products for global markets. With smart design and testing, you can avoid costly mistakes and get your industrial networking equipment to market faster.
Common Causes of EMC, EMI and ESD Issues in Product Design
To meet international standards, you need to understand what can cause electromagnetic interference and electrostatic discharge in the first place.
Poor shielding is a major culprit. If you don’t shield components that generate high-frequency signals, the emissions can interfere with other devices. Shielding individual components or the entire product helps contain these signals.
Inadequate grounding also allows EMI and ESD to wreak havoc. A good ground provides a path for stray electrical charges to escape, rather than building up or creating interference. Multiple ground points and ground planes are often needed in complex products.
Unprotected I/O ports are easy access points for EMI and ESD. Anyplace signals go in or out of a product, like USB, Ethernet or serial ports, needs EMI/ESD protection built in. Filters, transient voltage suppressors and opto-isolators are common solutions.
High-speed signals need containment. Fast digital signals, like in USB, HDMI or PCIe interfaces, generate significant EMI. Proper termination, shielding, filtering and layout practices help prevent issues.
PCB layout matters more than you think. How you lay out your PCB impacts both emissions and susceptibility. A messy layout with long trace runs acts as an antenna, while a clean layout with short traces helps contain signals. Ground planes, layer stacking and component placement all play a role.
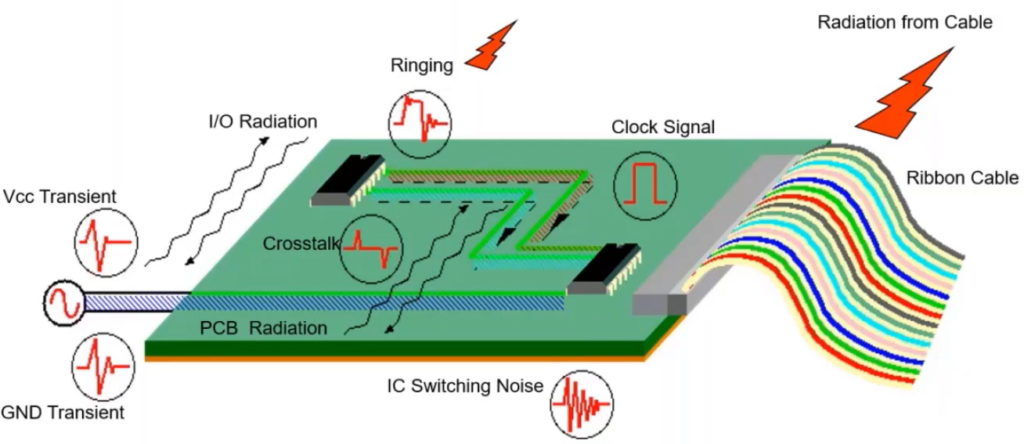
Figure 1 : Noise sources on a PCB
Source: https://etn-peter.eu/2022/08/23/emc-at-pcb-level-potential-sources-compliance-and-layout-techniques/
Effective Shielding Techniques Against EMI/EMC Problems
Shielding One of the most effective ways to reduce EMI is through shielding. Shielding physically blocks electromagnetic fields using conductive materials like steel, aluminium or copper. The shielding encloses the product and guides the fields around it. Shielding is commonly used for cables, connectors, enclosures and printed circuit boards. The most effective shielding uses a closed metallic enclosure, but shielding one or more sides can also help.
Cable Shielding
Shielded cables have an outer conductive layer like braided copper that blocks interference. Coaxial and shielded twisted pair cables are commonly used for shielding in networking equipment. The shielding should be grounded properly for maximum effectiveness. Unshielded cables act as antennas and can pick up significant amounts of EMI.
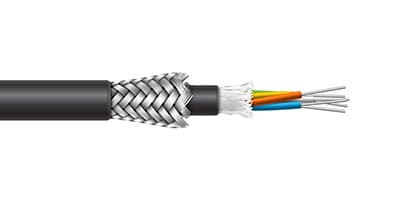
Figure 2: Cable Shielding
Connector Shielding
Shielded connectors contain conductive shielding, often in the form of metal shells or backshells, that enclose the connector housing. The backshells are typically threaded or clamped to the cable shielding to provide complete shielding continuity. Standard shielded connectors like BNC, SMA and Type N are commonly used on networking equipment.
Grounding
For shielding to work properly, it must be grounded. Grounding provides a path for the electromagnetic fields to flow to the ground. Without grounding, the fields can still enter the product where the shielding is not grounded. Multi-point grounding, with low-impedance connections to the ground, is the most effective approach.
Filtering
Filters are electronic components that block specific frequencies while allowing others to pass. Common types of EMI filters include capacitors, inductors and ferrite beads. Filters are often used in combination with shielding for maximum EMI reduction. They can be installed on cables, power supplies, and circuit boards. Proper grounding and shielding help maximize the effectiveness of filtering.
Using a combination of these techniques will significantly improve the EMI/EMC performance of networking equipment and help achieve compliance with international standards. Shielding, grounding and filtering should be designed into the product from the start for best results. Retrofitting products after design can be difficult and may require compromises in performance. Considering EMC at the beginning of the design process is the key to success.
ESD Protection Strategies for Robust Industrial Networking Products
As an industrial networking equipment manufacturer, protecting your products from electrostatic discharge (ESD) should be a top priority. ESD can wreak havoc on sensitive electronics, potentially causing permanent damage to components and circuitry. Following proper ESD protection strategies during design and manufacturing will ensure your products meet industry standards and have a long, reliable lifespan.
When designing your product, choose ESD-resistant components and materials. Look for parts, cables, and connectors that specifically mention ESD protection or conductivity. Metal enclosures and shielded cabling can also help prevent ESD buildup. During assembly, use anti-static wrist straps, mats, and grounding to dissipate static charge from technicians and equipment.
Once built, robust product enclosures and shielding provide an essential layer of defence. A conductive metal chassis or enclosure should be properly grounded to disperse any ESD before it reaches internal components. You might also install ESD-resistant gaskets, filters, and shielding on ports, connectors and any openings in the enclosure.
For networking equipment in particular, Ethernet ports and fiber optic connections require special attention. Look for Ethernet ports, transceivers and cables with built-in ESD protection to withstand network voltages and static discharges. Fiber optic connections should have grounded and shielded cabling as well as ESD-protected couplers and adapters.
Finally, be sure to test your product’s ESD resilience before releasing to market. Conduct air and contact discharge tests following IEC 61000-4-2 to ensure it can handle ESD strikes of 4, 8 and 15kV without issue. Testing will identify any weak points in your ESD protection so you can make necessary improvements.
With comprehensive strategies implemented at the design, manufacturing and testing stages, you can release industrial networking products that are hardened against ESD and built to last. Your customers will appreciate equipment that is engineered to withstand the demands of harsh environments and continue operating reliably for years to come.
EMC Compliance Testing: Ensuring Your Product Meets Global Standards
As an industrial networking equipment manufacturer, ensuring your products meet electromagnetic compatibility (EMC) standards is crucial. These regulations exist to guarantee that electronic devices can operate as intended in their electromagnetic environment without causing or experiencing interference.
To sell your equipment internationally, complying with standards like FCC in North America, CE marking in Europe, and VCCI in Japan is mandatory. While meeting each region’s specific limits, they share the same goal of minimizing electromagnetic interference (EMI). EMI refers to the unintentional generation, propagation and reception of electromagnetic energy that can potentially disrupt, degrade or limit the effective performance of electronic equipment and systems.
To test for compliance, your products go through a series of emissions and immunity tests. Emissions tests measure the electromagnetic energy emitted by your device, ensuring it stays within acceptable limits. Immunity tests assess your product’s ability to function properly in the presence of electromagnetic disturbances. Your equipment may be subjected to radiofrequency electromagnetic fields, electrostatic discharge (ESD) and electrical fast transients to simulate interference from the environment.
While achieving EMC compliance does require an investment of time and resources, it allows you to access new markets and gives your customers peace of mind. Partnering with an accredited EMC testing lab can help streamline the process. They have the specialized equipment, anechoic chambers and experienced technicians to thoroughly evaluate your product against the required standards.
EMC compliance may seem complicated, but breaking it down into manageable steps makes it less daunting. Focusing on good design practices, selecting appropriate components, minimizing emissions and maximizing immunity, getting early testing feedback, and working with experts when needed will set you on the path to compliance. Your customers and the company’s bottom line will thank you.
Conclusion
You now have the inside scoop on EMC, EMI, and ESD. Don’t let these acronyms scare you. With some thoughtful design considerations, you can create industrial networking products that play nice with others. Remember, radiated emissions and static discharge can wreak havoc if left unchecked. Do your homework, look to the standards, and test, test, test. Your customers will thank you when your product passes regulatory approvals with flying colors. When it comes to emissions, compliance is key. Now go design something great!